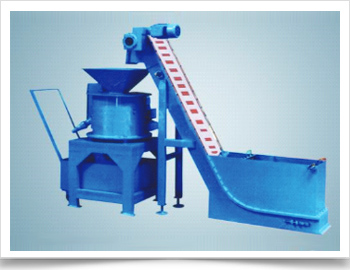
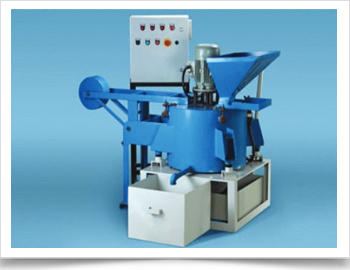
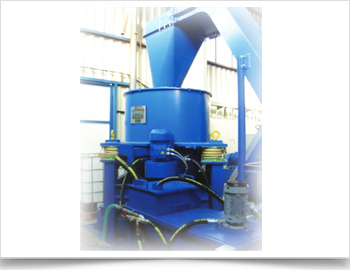
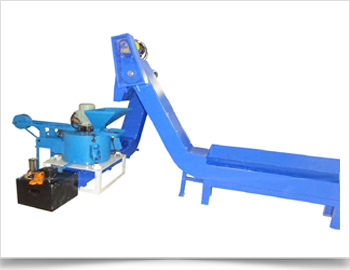
|
Chip wringer helps reduce the wastage of coolant oil. It can extract the coolant oil remains stuck to metal chips generated during machining processes. The rotating bowl of the chip wringer creates enough centrifugal force for solid-liquid separation. Oil is extracted through the bar screen and collected in a tray for reuse. This is a very cost-effective solution for drying chips too. In most applications, 99% of the coolant is reclaimed with this system. The chip wringer is recommended to be integrated with a chip conveyor for an easy and automated chip handling process.
Several machining processes such as broaching, hobbing, gun drilling, turning on single stuck to metal chips generated during cutting by the principle of adhesion and surface tension. The chips are generally stored in a chip yard. The oil mixed in with the chips drains due to gravity. However, the oil stuck (due to the principle of dhesion and surface tension) remains with the chips and gets disposed as waste. This results in direct nancial loss from wasted oil. Oil being a natural resource is wasted when the same can be recovered and reused. The chips, when being dried (due to the presence of oil) also pollutes the air causing environmental concerns.
Working : A hopper is provided at the top of the chip wringer to collect the metal chips from machining centers or chip conveyors. These chips, mixed with oil are collected in a basket. A timer value can be set on the control panel to start the chip wringer operation. By starting the system, the basket rotates and by centrifugal action, the oil gets separated from the chips. The oil collects in a tray while the dry chips remain in the basket (trolley). Once the system is automati-cally stopped as per the preset timer, the bottom section of the basket is opened and dry chips are collected into a trolley or a chip conveyor mecha-nism. The main components of proposed chip wringer are hopper, motor, basket, oil tray, body and control panel. In the above system, the metal chips from machining centers can be collected in a chip conveyer and are transported to the chip wringer. The chip wringer can be placed under or next to the end of the chip conveyer. Chips are dropped into the chip wringer at pre-set intervals.
Chip Wringer System
• Extraction of coolant from chips
• Principle of adhesion and surface tension
• Cost - effective method
• Low maintenance system
• Reduces wastage of coolant oil
|