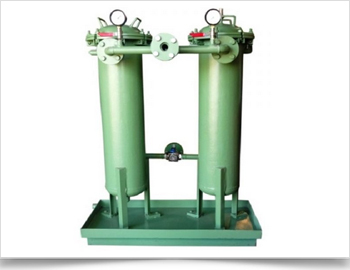
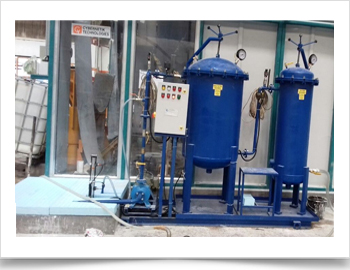
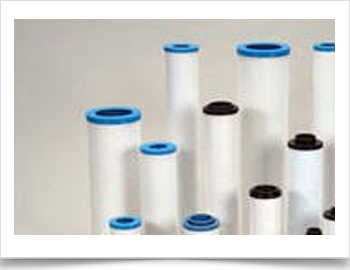
|
Pressure filter housings are pressure vessels in which cartridge/bag filters are assembled. These filters can be of various micron ratings, ranging from 350 microns to 1 micron. They are suitable for different types of fluids such as water-based emulsion, cutting oils or washing fluids. These filter housings are made of carbon steel or stainless steel and have been tested to withstand extreme pressures.
The dirty inlet is connected to the inlet of the housing. The fluid passes through the cartridge/bag filter where the dirt gets trapped and the clean fluid flows out from the outlet flange. A pressure sensor gives an indication when the cartridge/bag chokes.
Cartridge Filter : Cartridge filters are fabric or polymer-based filters that are affixed to a central core. They are usually rigid or semi-rigid and are disposable and easily replaceable. There are three basic types of depth cartridge construction: Resin-bonded, thermally bonded micro-fibre, and string wound. All three types have the same working principle—liquid under pressure is forced through the cartridge and exits through one end. Since the fluid moves from outside to inside, debris is collected mostly on the outside surface of the cartridge.
Bag Filter : Bag filters are fabric filters that are generally made of three types of media: mesh, melt-blown, or needled felt. They are usually non-rigid, disposable, and easily replaceable. Bag filters catch all dirt inside the bag where it is completely removed from the filter vessel during a change-out. An advantage of using a bag filter is that they have a much larger surface area which offers a wide-open flow path in as compared to cartridge filters. Bag filters have lower start-up differential pressure, hence offering longer run times.
• Filter vessels with cartridge elements or bags
• Flowrate variesas per the application
• 8 to Several 1000 LPM
• Suitable for very fine filtration - downto 0.2micron.
Cartridgeelementsselectionbasis :
• Micronrange
• Flowrate
• Mounting(flatorthreadedbase)
|
Advantages :
• Easy and systematic scrap management
• Low maintenance and no supervision required
• Cleaner shop
• Viable option for large facilities
• Different material chips (cast iron, aluminium, steel) can be processed
Applications :
• Most applications listed on the conveyor type applies to centralized system, as they are mainly used to handle chips generated from a group of machines.
|